
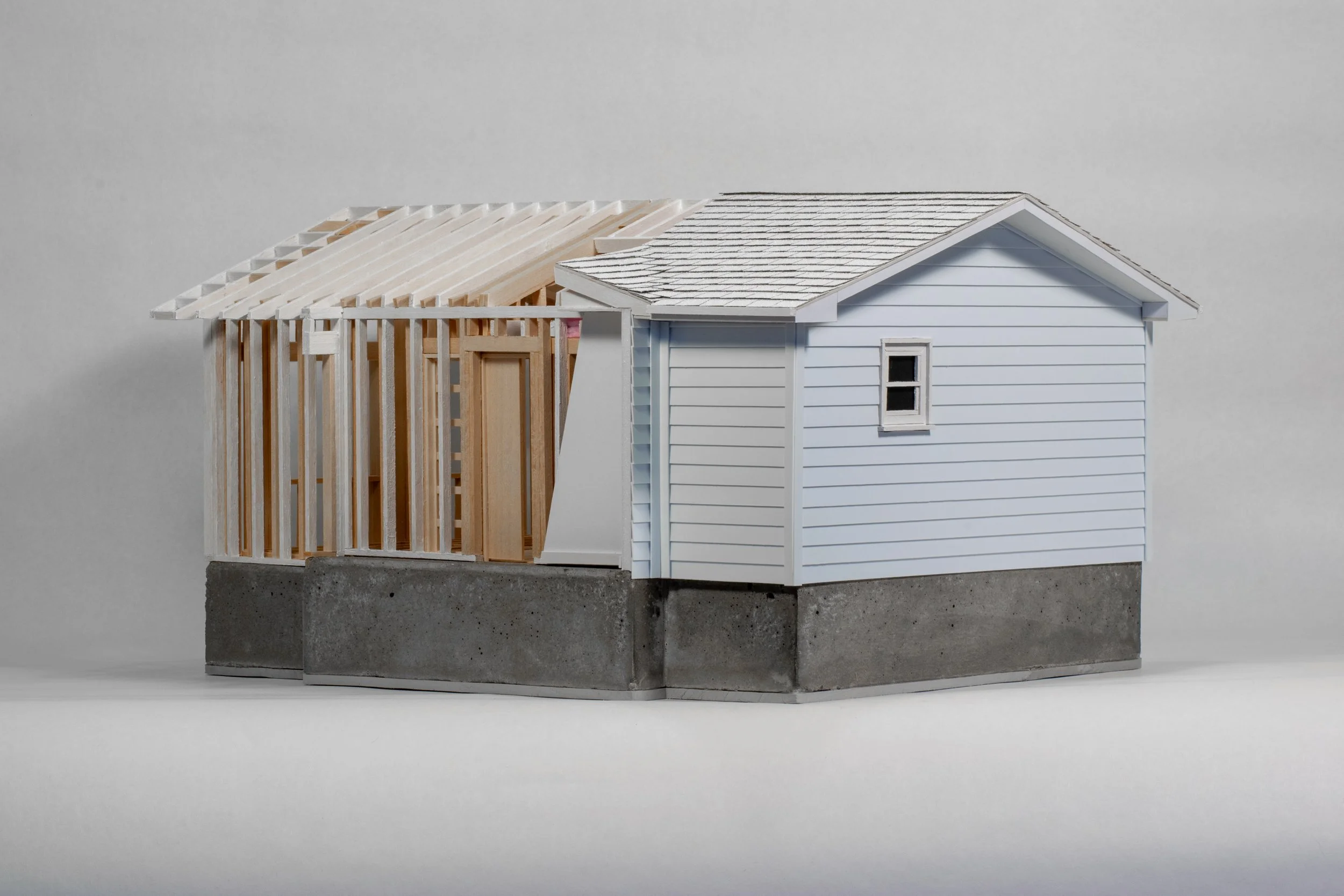

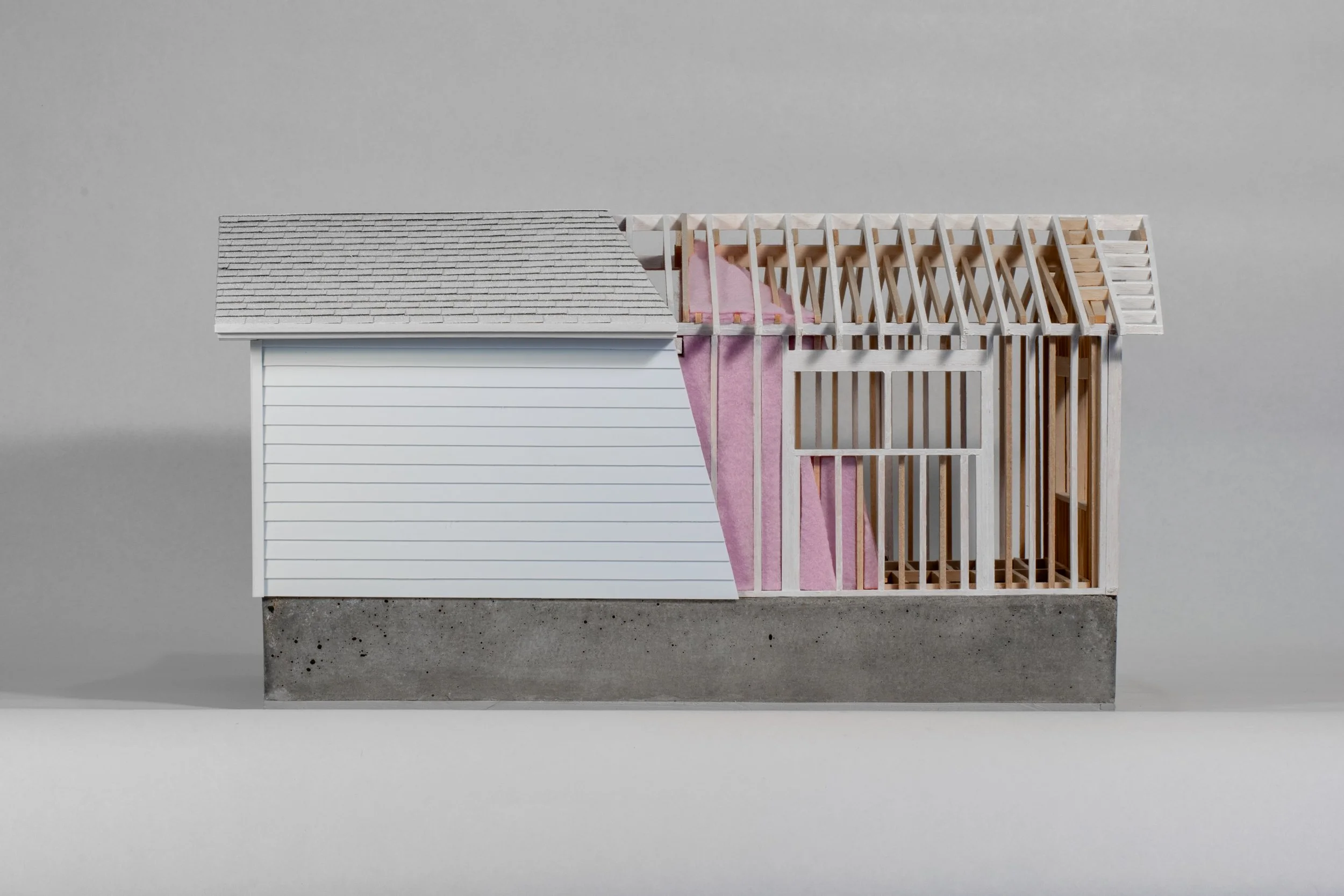

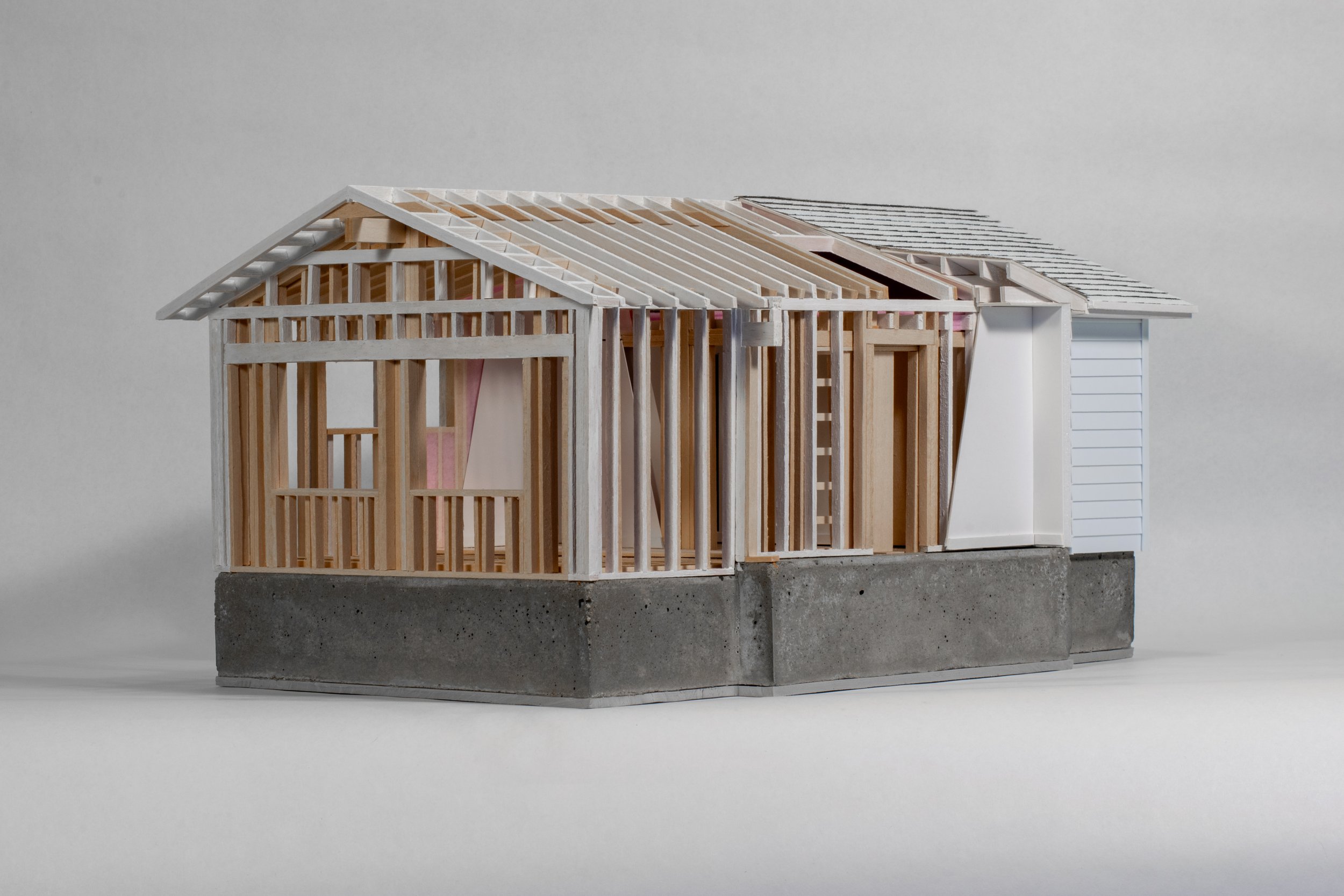
INTERIOR ADDITION
DETAILING A ROOM INSIDE OF A ROOM
Rising construction costs, a seller’s real estate market, Covid-era interest rates, growing families, and HGTV messaging have given rise to a peculiar home DIY renovation trend:
the garage-to-living space conversion.
This one-to-one build-out strategy offers homeowners the opportunity to increase the value and function of their home without the burdens of adding square footage, re-allocating interior spaces, or the fuss of large-scale architectural design. Unbeknownst to many homeowners in our region, this particular upgrade is governed by strict code-mandated regulations for energy efficiency, structural aptitude, and comprehensive building sciences.
To advocate for the value of your neighborhood Architect, we exhibit a design-less model of monotonous code extrapolation, existing deficiencies, and the excessive architectural duplication that negotiates between the two.
IECC R502.2: Change in space conditioning.
“Any unconditioned or low-energy space that is altered to become conditioned space shall be required to be brough into full compliance with this code.”
SPACE INSIDE OF SPACE
Resting as an effortless monolith in the room, the walk-behind closet is the only notable spatial intervention. It both right-sizes the two car garage into a useable bedroom scale, and provides the perceived resale value of couples walk-in closets.
A CEILING INSIDE A ROOF
Dominant real-estate trends demand a vaulted cathedral ceiling in any contemporary bedroom.
IRC R802.2 [Wood Roof Framing] Design and construction.
“The roof and ceiling assembly shall provide continuous ties across the structure to prevent roof thrust from being applied to the supporting walls.”
Rendered obsolete by removing the existing ceiling, the existing roof rafters are internally re-structured by a ridge beam and posts spanning the length of the room. New sloped ceiling joists are framed to underside of beam.
IECC TABLE R402.1.2: MAXIMUM ASSEMBLY U-FACTORS
Maximum ceiling U-factor = .026
That miniscule number equates to nearly a foot of insulation thickness, achieved here in three layers of R-15 batts. The sloped ceiling joists are then offset from roof rafters to eliminate thermal bridging.
IRC R806.1 [ROOF VENTILATION] Ventilation required.
“Enclosed rafter spaces formed where ceilings are applied directly to the underside of roof rafters shall have cross ventilation for each space…”
With the ceiling stuffed like a build-a-bear, vented soffits and wind baffles are a necessity to allow airflow beneath the roofing system and mitigate potential moisture buildup, ice damming, and shingle deterioration.
WALLS INSIDE OF WALLS
Under today’s energy codes, new construction exterior walls are typically designed with continuous insulation on the outside of the wall studs. Without replacing the existing siding, the existing walls must instead be ‘furred out’ on the interior to achieve the necessary wall depth for insulation.
IECC TABLE R402.1.2: MAXIMUM ASSEMBLY U-FACTORS
Maximum Wood Frame Wall U-Factor = .045
Translation: ~7 inches of insulation thickness, achieved here in two layers of R-13 Batt insulation. The existing exterior 2x4 stud wall is infilled with insulation and a new insulated 2x4 ‘furring’ wall is constructed inboard. Effectively a second exterior wall…interior. New wall studs offset from existing studs to eliminate thermal bridging.
IECC R702.7 Vapor retarders.
“Class I or II vapor retarders are required on the interior side of frame walls…”
IECC TABLE R402.4.1.1 AIR BARRIERS
“General requirements: A continuous air barrier shall be installed in the building envelope. Breaks or joints in the air barrier shall be sealed.”
Faced-type batt insulation on the interior-most surfaces of new stud walls (and ceilings) prevents condensation of humid interior air inside the wall cavity.
IRC R602.7.5 Supports for headers.
“Headers shall be supported on each end… The full-height stud adjacent to each end of the header shall be end nailed to each end of the header…”
In this case, the existing garage door framing was not observably braced by code-required full-height studs. Wind-resistant design was not a priority of the 1950s. To provide bracing for peak wind loads at the new window openings, a new full-height structural stud wall is laminated behind the existing garage door wall.
A FLOOR INSIDE A FLOOR
Garage floors are built to support a car, but a thick concrete pad doesn’t equate to the performance required under conditioned living space. Exposed to years of abuse, freeze-thaw cycles, base-layer settling, or simply vintage installation (asphalt in this case), these uninsulated/uneven monoliths are less than ideal for supporting your forever-home’s dream getaway suite.
IECC TABLE R402.1.3: INSULATION MINIMUM R-VALUES
Minimum Slab-on-Grade R-Value = R-10, 4’ from edge
IRC R506.2.3 Vapor retarder.
“A… vapor retarder… shall be placed between the concrete floor slab and the base course…”
Two things any garage floor is without: insulation and vapor barrier. The lack of thermal/moisture protection combined with the probability of a busted slab means a complete floor replacement is the right renovation. Here, the asphalt is removed, new insulated concrete slab-on-grade installed (~10” thick assembly), and the finish floor is raised on 2x ‘joists’ to infill the existing gas curb step. The result is two new floors for the function of one.
**The information provided above is based on the applicable codes as adopted by the local authorities at a specific moment in time, located in a specific region, for a specific owner. References to code language are for rhetorical purposes only and shall not be considered transferable to another jurisdiction, client, location, or owner. Technical detail information listed is based on services rendered to our client and shall not be considered as services rendered to another individual… again it’s all rhetorical folks.